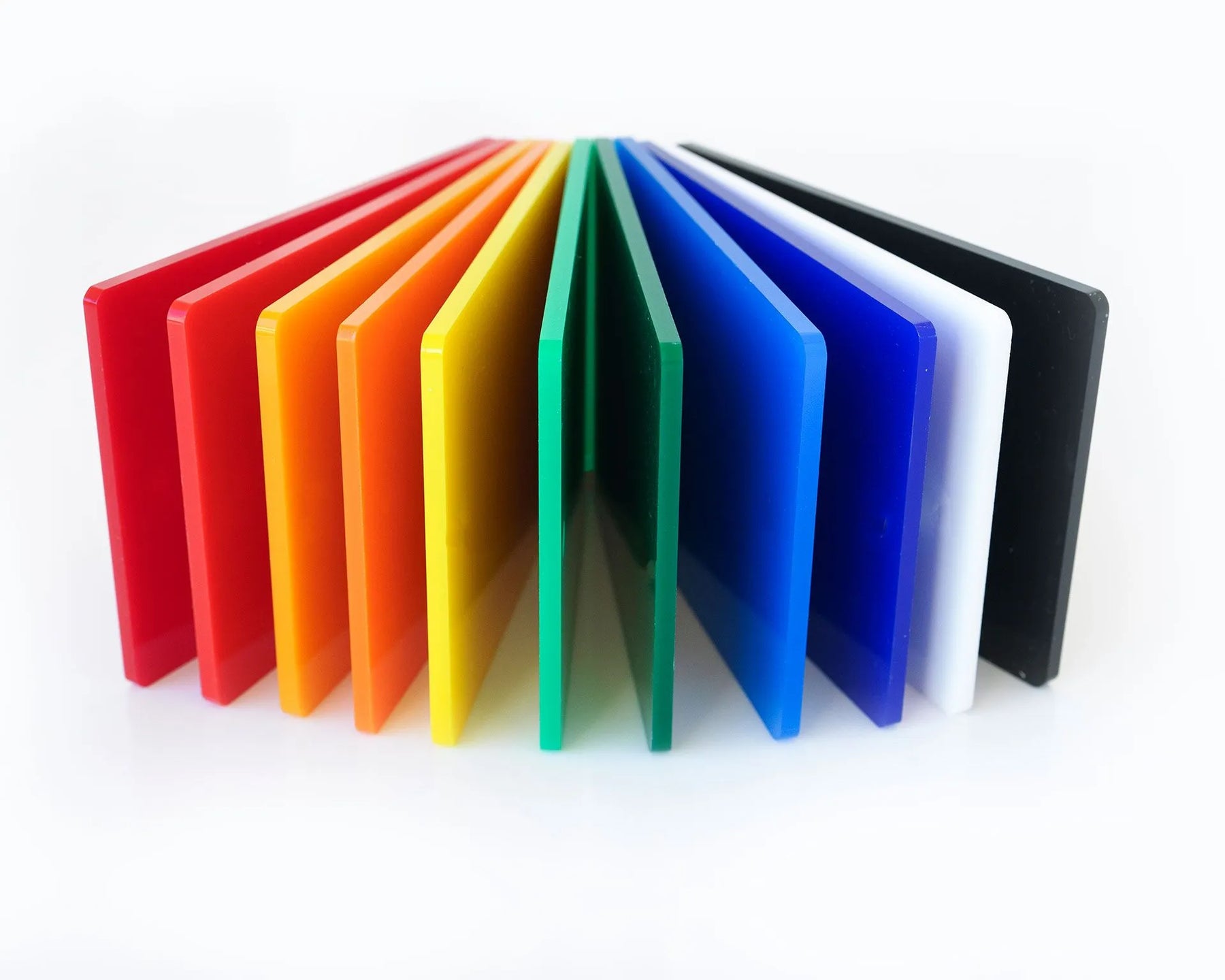
Acrylic Laser Cutting and Engraving 101: A Beginner's Guide
Welcome to the World of Acrylic Laser Cutting and Engraving
Acrylic laser cutting and engraving open up a realm of creative possibilities, blending technology and artistry to produce stunning results. Whether you are a hobbyist, a professional designer, or an entrepreneur, mastering the craft of laser cutting and engraving on acrylic can elevate your projects to new heights. This guide aims to demystify the process, offering insights and tips to get you started on your journey.
Why Acrylic is a Popular Choice for Laser Projects
Acrylic is a favored material in the world of laser cutting and engraving due to its versatility, durability, and aesthetic appeal. Its ability to mimic glass while being lighter, safer, and more cost-effective makes it a go-to choice for many creators. Additionally, acrylic comes in a variety of colors and finishes, adding to its desirability for a wide range of projects.
Overview of What This Guide Will Cover
In this guide, we will explore the fundamental aspects of working with acrylic, from understanding its types to choosing the right tools, setting up your laser cutter, and executing precise cuts and engravings. We'll also delve into advanced techniques and offer creative project ideas to inspire your next masterpiece.
Table of Contents:Β
Β

Understanding Acrylic
Types of Acrylic: Cast vs. Extruded
Acrylic is available in two primary forms: cast and extruded. Cast acrylic is made by pouring liquid acrylic into molds, resulting in sheets that are harder and more scratch-resistant. It is preferred for engraving due to its superior quality and clearer edges. Extruded acrylic, on the other hand, is formed by pushing acrylic pellets through a mold. It is softer and less expensive but can produce a frosty edge when cut, making it less ideal for intricate designs.
Advantages of Using Acrylic for Laser Cutting and Engraving
Acrylic offers several advantages, including clarity, flexibility, and strength. It cuts cleanly, leaving smooth edges that often require minimal post-processing. Additionally, its transparency allows for unique lighting effects, especially when edge-lit with LEDs. Acrylic's resilience against weathering makes it suitable for both indoor and outdoor applications.
Common Applications of Acrylic Projects
Acrylic is used in a multitude of projects, from signage and awards to jewelry and home dΓ©cor. Its versatility allows for the creation of intricate designs and functional items. Common applications include retail displays, light fixtures, custom art pieces, and personalized gifts, each benefiting from acrylic's distinctive properties.
Laser Cutting vs. Laser Engraving
Definitions and Differences
Laser cutting and engraving are two distinct processes. Cutting involves slicing through the material to create shapes and outlines, whereas engraving involves etching the surface to add patterns, text, or images. Understanding the differences is crucial for selecting the right technique for your project.
When to Choose Cutting Over Engraving
Choosing between cutting and engraving depends on the desired outcome. Cutting is ideal for creating parts that need to fit together, such as puzzle pieces or structural components. Engraving is perfect for adding decorative elements, intricate designs, or personalized details to a surface without altering its structural integrity.
Pros and Cons of Each Technique
Laser cutting provides clean, precise edges but can be limited by material thickness. Engraving, while versatile in adding detailed designs, can be time-consuming and requires careful attention to detail. Both techniques have their merits, and the choice often depends on the specific requirements of the project.

Preparing for Your Project
Choosing the Right Type of Acrylic
Selecting the appropriate type of acrylic is the first step in any project. Consider factors such as thickness, color, and finish. Cast acrylic is preferred for its clarity and quality, while extruded acrylic may be suitable for less demanding applications or where budget constraints exist.
Essential Tools and Materials
Apart from the laser cutter, essential tools include a computer with design software, a cutting mat, safety glasses, and proper ventilation. Having a variety of acrylic sheets in different colors and thicknesses can also be beneficial.
Safety Precautions and Best Practices
Working with laser cutters requires strict adherence to safety protocols. Always wear protective eyewear, ensure adequate ventilation to avoid inhaling fumes, and never leave the machine unattended while in operation. Regular maintenance and calibration of the laser cutter are essential for safe and efficient use.
Setting Up Your Laser Cutter
Selecting the Appropriate Laser Cutter for Acrylic
Choosing the right laser cutter involves considering factors such as power, bed size, and software compatibility. CO2 lasers are commonly used for cutting and engraving acrylic due to their precision and efficiency.
Initial Setup and Calibration
Setting up your laser cutter involves assembling the machine, installing necessary software, and calibrating the laser. Calibration ensures the laser is aligned correctly, which is crucial for achieving precise cuts and engravings.
Maintenance Tips for Optimal Performance
Regular maintenance of your laser cutter includes cleaning the lenses, checking the cooling system, and ensuring the laser tube is functioning properly. Routine checks and maintenance help in prolonging the machine's lifespan and maintaining high-quality output.

Designing Your Project
Creating Your Design: Software Options and Tips
Design software like Adobe Illustrator, CorelDRAW, and Inkscape are popular choices for creating laser cutting and engraving designs. These programs allow for detailed vector and raster designs, essential for different aspects of your project.
Vector vs. Raster Designs: What You Need to Know
Vector designs are composed of paths and points, making them ideal for cutting and outlining shapes. Raster designs consist of pixels, suitable for detailed engravings like photos or intricate patterns. Understanding the difference is key to preparing your files correctly.
Importing and Preparing Files for Laser Cutting and Engraving
Once your design is ready, import the file into the laser cutter's software. Ensure the settings match your project's requirements, such as power, speed, and resolution. Proper file preparation ensures smooth and accurate execution.
Cutting Acrylic
Step-by-Step Guide to Cutting Acrylic
- Choose the appropriate acrylic sheet.
- Place the sheet on the laser cutter bed.
- Import your design file.
- Adjust the settings (power, speed, frequency).
- Conduct a test cut on a scrap piece.
- Execute the cut, monitoring the process.
Optimal Settings for Different Thicknesses
Settings vary based on acrylic thickness. Thicker sheets require higher power and slower speeds. For example, a 1/8" sheet might need 50% power at 30% speed, while a 1/4" sheet may require 80% power at 20% speed. Testing and adjusting are crucial.
Troubleshooting Common Cutting Issues
Common issues include incomplete cuts, burn marks, and warping. Adjusting power and speed, ensuring the material is flat, and cleaning the laser lens can resolve many problems.
Engraving Acrylic
Step-by-Step Guide to Engraving Acrylic
- Select and secure the acrylic sheet.
- Import and prepare the engraving file.
- Set the laser's power, speed, and resolution.
- Conduct a test engraving.
- Execute the engraving, checking for consistency.
Optimal Settings for Detailed Engraving
For detailed engravings, lower power and higher speed settings are recommended. For instance, 20% power at 80% speed can achieve fine details without excessive depth.
Tips for Achieving High-Quality Engravings
Use high-resolution images for clarity, ensure the acrylic surface is clean, and perform multiple light passes for depth without overburning.
Post-Processing Techniques
Cleaning and Polishing Acrylic Edges
After cutting, edges may need polishing for a smooth finish. Flame polishing, using a heat gun, or sanding with fine-grit sandpaper can enhance the clarity and smoothness of edges.
Removing Residue and Smoke Marks
Residue and smoke marks can be removed using isopropyl alcohol and a soft cloth. For stubborn marks, a mild detergent and water solution may be effective.
Finishing Touches for a Professional Look
Finishing touches like edge painting, mounting hardware, or adding lighting elements can elevate the final appearance of your project, giving it a polished and professional look.
Common Challenges and How to Overcome Them
Dealing with Warping and Melting
Warping can be minimized by using a honeycomb bed or a vacuum table to hold the material flat. Reducing laser power and making multiple passes can prevent melting.
Avoiding Cracks and Breaks
Cracks and breaks can occur if the laser power is too high or the material is stressed. Proper material handling and using appropriate settings are essential.
Ensuring Consistent Results
Consistency is achieved through regular machine maintenance, proper material storage, and meticulous file preparation. Testing and fine-tuning settings for each project also help in maintaining uniformity.

Creative Project Ideas
Inspirational Examples of Acrylic Laser Projects
From intricate jewelry to elaborate light fixtures, the possibilities with acrylic are endless. Explore projects that push the boundaries of creativity and functionality.
DIY Home DΓ©cor Ideas
Create custom home dΓ©cor items like wall art, coasters, and photo frames. Personalized pieces add a unique touch to any space.
Personalized Gifts and Custom Creations
Design and produce personalized gifts such as nameplates, keychains, and awards. Custom creations are perfect for special occasions and memorable keepsakes.
Advanced Techniques
Layered Acrylic Projects
Layering different colors and thicknesses of acrylic can create stunning visual effects and depth. Experiment with multiple layers to add complexity to your designs.
Combining Acrylic with Other Materials
Incorporate materials like wood, metal, or fabric into your acrylic projects. The combination of textures and finishes can result in unique and innovative creations.
Exploring 3D Effects with Engraving
Engrave at varying depths to achieve 3D effects. This technique can add dimension and realism to your engravings, making your projects stand out. By carefully adjusting the laserβs power and speed settings, you can create intricate layers that mimic a three-dimensional look, adding depth and sophistication to your designs.
Leave a comment